Emergency shutdown (ESD) valves play a pivotal role for isolating flow equipment in an emergency situation thus assuring the safety of plant and civilian personnel, the protection of assets, and the mitigation of any potential environment events.
Whether a specific shutdown valve application has been formally designated to a SIL (Safety Integrity Level) status or has been identified as being “critical” through a HAZOP process, an ESD system has the role of delivering the optimal reliability performance, by operating without question when called upon.
Choosing the best and most suitable ESD solution for your process application is often a challenge. The challenges become greater when there are limits impacting ESD valve applications: Limitations of power or space, operating large valves with high output torques, along with factoring in the reliability of your own plant’s infrastructure (e.g., air, electricity, control system).
Visit EHO Product Page
Choosing the best and most suitable ESD solution for your process application is often a challenge. The challenges become greater when there are limits impacting ESD valve applications: Limitations of power or space, operating large valves with high output torques, along with factoring in the reliability of your own plant’s infrastructure (e.g., air, electricity, control system).
Visit EHO Product Page
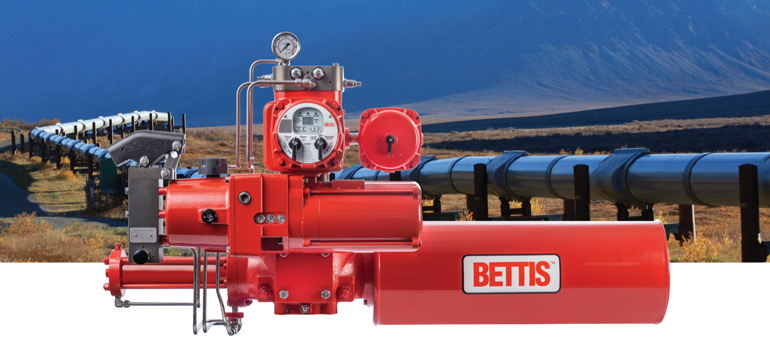
For critical quarter-turn high torque valves, or in areas where plant air isn’t available, electric actuators have been the primary means of actuation. Although having the ability to deliver high torques, they do pose issues that have to be considered for a SIL rating or through the HAZOP process. The electrical source reliability must also be factored. With electric actuators and their need for gearing, the mechanical means to drive to a fail-safe position and the inherent time/speed to get into fail-safe position is a costly and complex feat. The use of an electro-hydraulic actuator in these applications over-comes the limitations of electric actuator gearing, but this type of installation has typically required a separate hydraulic pressure skid, which introduces more potential failure points and makes for a complex installation as well.
A modern self-contained electro-hydraulic actuation solution (EHO)addresses these issues, and provides a reliable, cost-effective ESD solution by utilizing a quick, dependable spring-return actuator providing a fail-safe stroke combined with an internal hydraulic power pack and electronic control module. Figure 1 shows the components of an EHO system.
A modern self-contained electro-hydraulic actuation solution (EHO)addresses these issues, and provides a reliable, cost-effective ESD solution by utilizing a quick, dependable spring-return actuator providing a fail-safe stroke combined with an internal hydraulic power pack and electronic control module. Figure 1 shows the components of an EHO system.
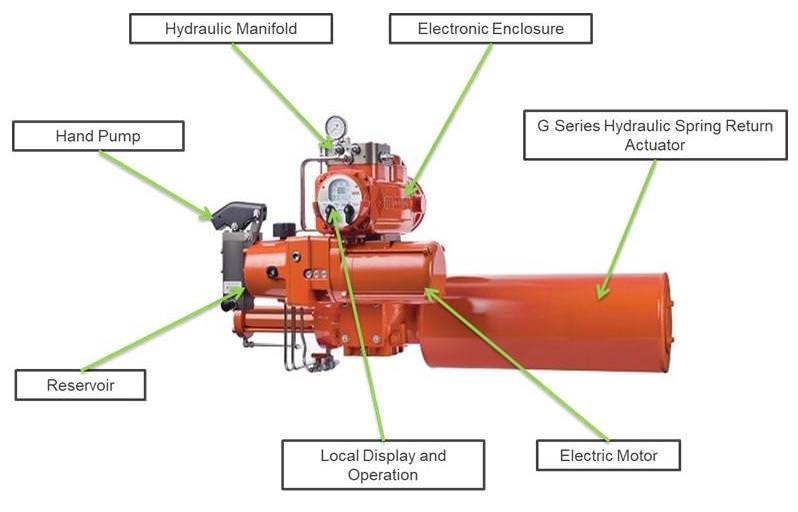
The key to the EHO design is the self-contained, onboard hydraulic reservoir. In the event of an emergency power loss, a manual hydraulic hand pump can be utilized so that the actuator can be stroked directly or to recharge an accumulator. For ESD applications requiring SIL 2 certification, an independent solenoid can be utilized within the actuator control scheme, providing fail-safe redundancy, as shown in figure 2:
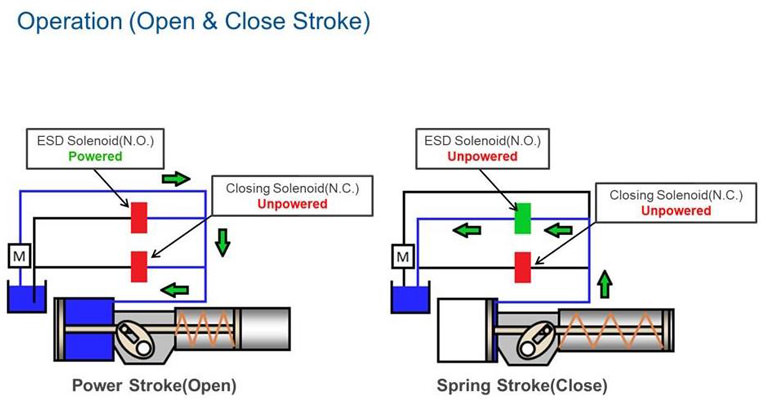
Figure 2
The use of an integral micro-processor-based controller allows for built-in EHO system self-diagnostics which continuously monitors your system for any abnormalities and will alert you if one arises. Figure 3 shows the construction of a controller which is designed to withstand harsh environments.
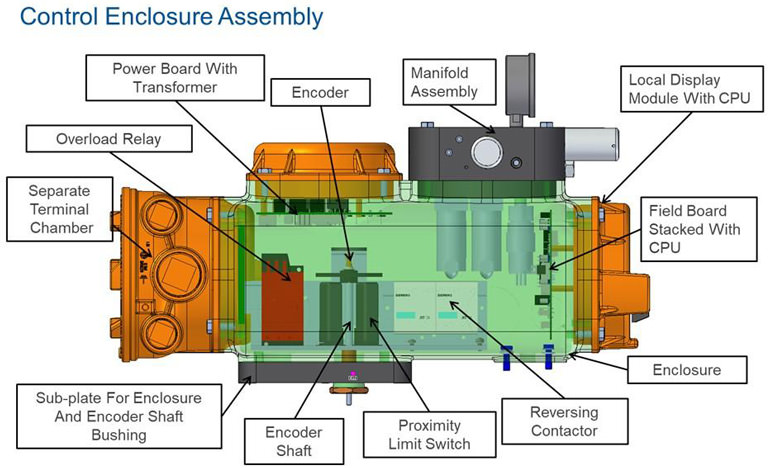
Figure 3
The utilization of a micro-processor based controller also allows for the execution of partial stroke tests. An emergency shutdown valve that has been service for several years without any operation, testing or maintenance might not work when it is needed. Therefore, testing and maintenance are a vital part of an ESD valve life cycle. Partial-stroke testing can be a great help to check the valve condition while the valve is in operation. With regards to SIL calculations, it has been demonstrated that partial stroke testing significantly lowers the Average Performance on Demand (PFDavg).
Seconds matter in isolating failures that can adversely impact people, communities and production assets. A self-contained Electro-hydraulic actuation system provides a reliable and fail-safe ESD solution designed to mitigate system risk, personnel injuries and reduce negative environmental impacts.
Visit EHO Product Page