While replicator parts initially may seem to cost less, you will pay more in the long run. This is due to a shorter life span, along with the additional risk of equipment failure, and poor performance caused by tolerance/specification issues.
This increases the potential for unplanned downtime, impacting safety and profitability. Only our original equipment manufacturer (OEM) parts are designed to the same exacting standards and utilizing the same materials as used in Emerson valve manufacturing plants around the world. And only with genuine OEM parts can you be sure of compliance with international codes, standards and approvals.
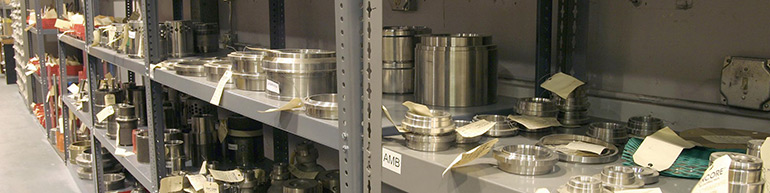
The Parts and Support You Need, When You Need Them
Increased availability of genuine OEM parts means improved levels of service. Cornerstone and Emerson have a network of local service providers and facilities. In addition to these local resources, the Emerson North American Parts Distribution Center is located in Cincinnati Ohio, with over 17,000 parts available to you 24/7.
Parts Assessment
Having the right mix and quantities of spare parts to maintain effective equipment operation and keep downtime in minimum is critical. By performing a plant walkdown, we can help you determine if you have the parts you need, in the proper quantities, to help ensure that your assets can be repaired cost-effectively and with minimum downtime. You will also have access to spare parts planning tools and serial number-based valve configuration data. These tools and databases help verify that the correct parts are on hand with reduced inventory investment.
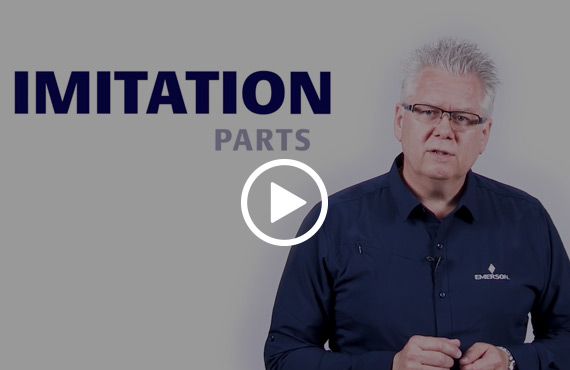
The Value of OEM Spare Parts
Plant Walkdown
A plant walkdown and follow-up assessment can help provide you with the following benefits:
- Gathering up-to-date information about your equipment to help ensure data is accurate and accessible during unplanned events.
- Determining replacement parts needs and availability
- Improving maintenance planning and efficiency
- Reaching a proper state of readiness for planned and unplanned events
- Identifying critical valve applications to effectively plan for diagnostic evaluations
- Improving cost management of your parts inventory
- Reducing downtimes by balancing stocking decisions based on valve criticality and parts lead time
Plan For Outage Success
An outage is always a balancing act between taking the time needed for proper service and getting the process or plant back online quickly. With proactive planning, it’s possible to set achievable goals, priorities, and service schedules to address all the adjustments, maintenance, repairs, upgrades, and optimizations your plant might need. Preparation begins months in advance of your next planned outage. We start by identifying your goals to help provide the right services, deliverables, and expectations that align to the scope, timing, duration, and budget of your outage. In addition to enjoying a more efficient outage, you will protect your valuable instrument and valve assets by working with a service provider that can restore them to original documented OEM standards.
Request Parts Quote
Request Parts Quote